By: Allie Shane, Communications Specialist
In a recent discussion with the Founder of Empathic Engineering, Emily Honor Hubbard shared the pivotal role of cultural understanding and collaboration in saving United States and Mexico manufacturers valuable time and thousands of dollars.
Laying the Foundation
Before graduating from California Polytechnic State University with a degree in mechanical engineering, Hubbard performed an independent study on the development of empathy in engineering students. During a 10-week rehabilitation engineering course, she observed an increase in empathy from engineering students based on its five constructs: affective response, affective mentalizing, self-other awareness, emotional regulation and perspective taking.
“I love being able to consider the constructs because we empathize so often. We go through this process [the five constructs] and if we don’t give ourselves time to go through the whole process, it gets cut short,” commented Hubbard.
Hubbard modeling how active listening is much easier when making eye contact and facing towards our coworkers.
Upon graduation, Hubbard began as a line worker assembling medical ventilators and later took a job at Ford Motor Company as an engineer on the Mexico team. At meetings with the U.S. team, the Mexico team would hardly participate in English discussion. After hanging up the call her team would solve a problem in Spanish.
“I’m sitting there and I’m like the other half of the team doesn’t know,” said Hubbard.
She shared a career move to the Milwaukee area that strongly informed her decision to begin Empathic Engineering.
“I worked at a company where I felt that people got so frustrated because of not understanding each other that I ended up feeling sick going into work…nothing had to get to the point that it did,” she said.
Across all three roles Hubbard arrived at the same conclusion: communication gaps exist in the workplace, and many of these gaps stem from peoples’ egos.
“It is our inability to break a wall that says, ‘well this person works on the line, or this person is younger than me or this person looks different so I’m just not going to ask them’,” said Hubbard.
Applying experience
By taking the five constructs of empathy used in her 10-week independent study and integrating Lean Six Sigma, a process improvement methodology that resonates with many engineers, Hubbard has created a 10-week course that educates U.S. and Mexico manufacturers on how to bridge communication gaps. “What I am working on is making sure that we understand how much people do affect our process and honestly, we take the time to have conversations,” she said.
To familiarize engineers with the course, Hubbard meets with teams once a week for three hours, giving a short lesson that utilizes experience-based learning. From there, she sits in on team meetings, using a rubric to score the team on communication, trust and innovation.
If the company is interested, Hubbard will use the empathy assessment index. Engineers fill out a short 10-minute questionnaire during an initial observation. The answers to the questionnaire give Hubbard insight into which empathy constructs have the most room for improvement throughout the 10-week period.
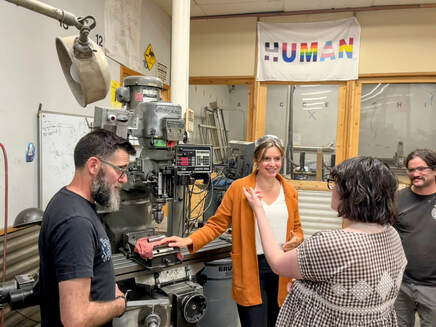
Hubbard modeling how active listening is much easier when making eye contact and facing towards our coworkers.
Creating Positive ChangeThe results are in the numbers. For example, Hubbard was able to save one client $70,000 through her three-day problem-solving workshop. Although her primary focus is on manufacturers based in the U.S. and Mexico, Hubbard hopes that this idea of communication presented through her course will expand well beyond the two countries.
Hubbard’s passion for effective communication in the manufacturing industry is not solely evident in her efforts at Empathic Engineering. She runs Milwaukee Manufacturing Meetup, a monthly gathering where local university students, industry professionals and other individuals interested in the manufacturing space can network, share knowledge and ask questions.
“I just know that I’m doing this because I have to and that’s why I’m so committed…when I work with a company it is because I lived the experience of not having a good communication structure at work,” said Hubbard.